KI in der Qualitätssicherung
Die fortschreitende Entwicklung und Integration von Künstlicher Intelligenz (KI) hat in diversen Branchen eine transformative Wirkung gezeigt. Insbesondere in Bezug auf die Qualitätssicherung bieten KI-basierte Systeme Potenziale für eine kosteneffiziente Qualitätssicherung in Produktionsprozessen. Prozesse wie Sicht- oder mechanische Prüfungen verursachen einen zusätzlichen Aufwand, der zu teurer Nacharbeit oder Ausschuss der Bauteile führen kann. Die akustische Prozesscharakterisierung für das Rührreibschweißen (Friction Stir Welding, FSW) ermöglicht einen vergleichsweise neuen Ansatz der Prozessüberwachung zur Erkennung von Schweißnahtunregelmäßigkeiten durch die Charakterisierung des emittierten Geräusches im hörbaren Frequenzbereich (Luftschallsignal). Eine Überwachung des Produktionsprozesses durch eine intelligente Kombination von Sensoren und anschließender Auswertung mittels KI ermöglicht nicht nur die echtzeitnahe Qualitätskontrolle, sondern auch das Erkennen und Zuordnen von Fehlern und somit eine direkte Rückkopplung zur gesamten Fertigungskette [1].
Was ist Rührreibschweißen?
Die beteiligten Prozessstufen (I bis V) des FSW-Verfahrens sind in Abbildung 1 dargestellt. Zu Beginn des Fügeprozesses wird das Werkzeug in Rotation versetzt (I) und taucht durch eine Abwärtsbewegung in das Werkstück ein (II). Während des Eintauchvorgangs nimmt die Axialkraft Fz zu und plastifiziert den Werkstoff durch die Reibungswärme. Während der Schweißphase (III) durchmischt sich das plastifizierte Werkstückmaterial durch Schulter und Stift des Schweißwerkzeugs und bildet eine feste Verbindung entlang der Schweißbahn. Am Ende des Schweißvorgangs (IV) wird die Bewegung des Werkzeugs zunächst gestoppt, während Schulter und Stift noch einige Sekunden lang in Rotation sind. Dann wird das Werkzeug mit einer Aufwärtsbewegung aus dem Fügebereich herausgefahren. Die so hergestellten Verbindungen zeichnen sich durch geringe Prozesszeiten, lokalisierten Wärmeeintrag mit geringer Querschnittsreduktion und minimiertes Auftreten von intermetallischen Phasen, da die Schmelztemperaturen der Werkstoffe nicht überschritten werden, aus [2].
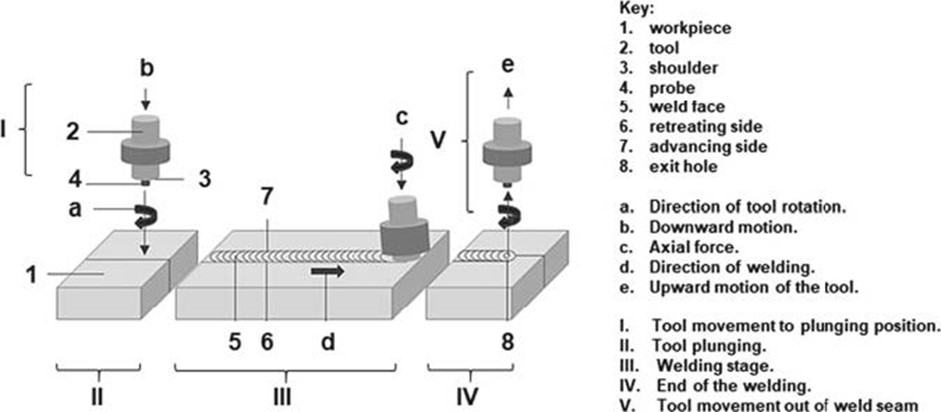
Vorteile von Luftschallsensoren
In bisherigen Veröffentlichungen wurde die akustische Detektion von Schweißnahtunregelmäßigkeiten meist auf der Basis von Körperschallsensoren durchgeführt. Obwohl eine Korrelation zwischen Schweißnahtfehlern und Körperschall nachgewiesen werden konnte, gibt es prozessbedingte Defizite beim Einsatz von Körperschallsensoren. Dazu gehören eine feste Einbauposition und die eingeschränkte Anwendbarkeit für großflächige Bauteile wie Batteriegehäuse. Im Gegensatz dazu können Luftschallsensoren (Mikrofone) direkt im Bereich des Fügeprozesses angebracht werden. Dies reduziert Einflüsse von Bauteilgröße, Fügewerkstoffen und Schweißnahtgeometrie. Es wurde gezeigt, dass die akustische Analyse zur Erkennung von Schweißnahtunregelmäßigkeiten wie z.B. Grat- und Hohlraumbildung geeignet ist. Alle Experimente wurden mit einer robotisierten FSW-Anlage durchgeführt, die durch ein selbst entwickeltes akustisches Messgerät modifiziert wurde.
Erstellung Trainingsdatensatz: Erzeugen von Schweißnahtunregelmäßigkeiten
Entscheidend für eine qualitativ hochwertige Schweißnaht durch den Rührreibschweißprozess ist der durch das Schweißwerkzeug erzeugte Materialfluss. Ist dieser durch ungeeignete prozessseitige Einstellgrößen und/oder eine unzureichende Konturierung des Rührreibschweißwerkzeuges aufgrund von zunehmendem Werkzeugverschleiß gestört, so kommt es im Laufe des Schweißprozesses zu Unregelmäßigkeiten wie beispielsweise übermäßiger Gratbildung oder der Bildung von Hohlräumen. Um gezielt Unregelmäßigkeiten in der Schweißnaht hervorzurufen, wurden, ausgehend von der Standardgeometrie, Anpassungen an der Geometrie des Schweißstiftes und der Schulter vorgenommen, welche die Durchmischung des plastifizierten Werkstoffes verringern und folglich die Bildung stochastisch auftretender Hohlräume hervorrufen. Geometrieänderungen resultieren in der industriellen Praxis oftmals aus Verschleißerscheinungen der Werkzeuge beim Schweißen längerer Nähte. Eine Simulation des Werkzeugverschleißes durch gezielte Anpassung der förderwirksamen Strukturen bildet somit die industriellen Rahmenbedingungen im täglichen Einsatz ab.
Im Rahmen des Projektes wurden aus diesem Grund Blindnähte in Halbzeugen der Aluminiumlegierung AlMg3 (EN AW-5754) erzeugt, welche zahlreiche Anwendung in der Elektromobilität und im Automobilbau findet. Abbildung 2 zeigt die verwendete Versuchsgeometrie, die sich aus einer L-Naht und einer Mäander-Naht zusammensetzt. Diese wurde zusammen mit der RRS Schilling GmbH entwickelt, um industrielle Anforderungen, wie beispielsweise das Schweißen von Kühlkörpern, bestmöglich abzubilden.
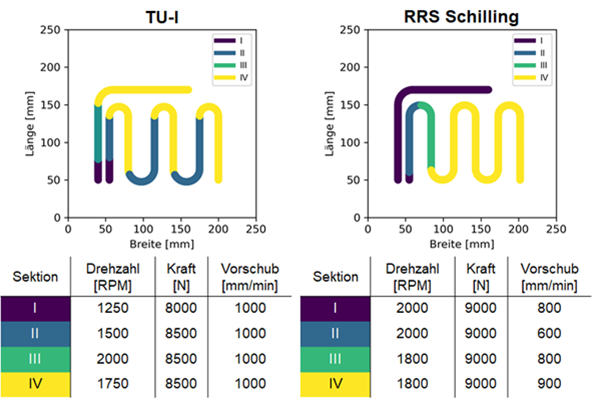
Erstellung Trainingsdatensatz: Detektion von Schweißnahtunregelmäßigkeiten
Im Anschluss wurden die Probenbleche mittels Röntgeninspektion zerstörungsfrei geprüft, um die Lage der Hohlräume im Blech zu erfassen. Mit Hilfe dieser Methodik in Kombination mit der zeitsynchronen Erfassung der Prozess- und Akustiksignale besteht die Möglichkeit, diese entstandenen Hohlräume direkt mit den erfassten Prozessdaten zu verknüpfen. Erste Analysen der akustischen Zeitsignale zeigten eine Abhängigkeit von der eingestellten Werkzeugdrehzahl n, da sich sowohl die Eigenfrequenz der Werkzeugdrehzahl als auch ganzzahlige Vielfache im Akustiksignal darstellen ließen. Drehzahlvariationen im Schweißprozess waren somit auch im Akustiksignal sichtbar. Ein im Rahmen des Projektes entwickelter Auswertealgorithmus ermöglicht die automatische Identifikation von Hohlräumen entlang des Schweißpfades als auch die Ausgabe der Positionen und Länge der Hohlräume im Probenblech, um eine reproduzierbare und objektive Bewertung der Blindnähte zu gewährleisten. Dies geschieht über die Einpassung des realen Schweißpfades in das Bild und die hierauf folgende Auswertung mittels Pixel Klassifikator (KI). Hierdurch wird die zerstörungsfreie und ortsaufgelöste Prüfung der Schweißnähte im Probenblech ermöglicht, um nachfolgend die Korrelation der akustischen Signale als auch der Prozessgrößen wie der Vorschub- und Querkraft und dem Spindelmoment mit der Schweißnahtunregelmäßigkeit „Hohlraum“ herzustellen. Eine grafische Repräsentation dieses Ergebnisses ist in Abbildung 3 dargestellt.
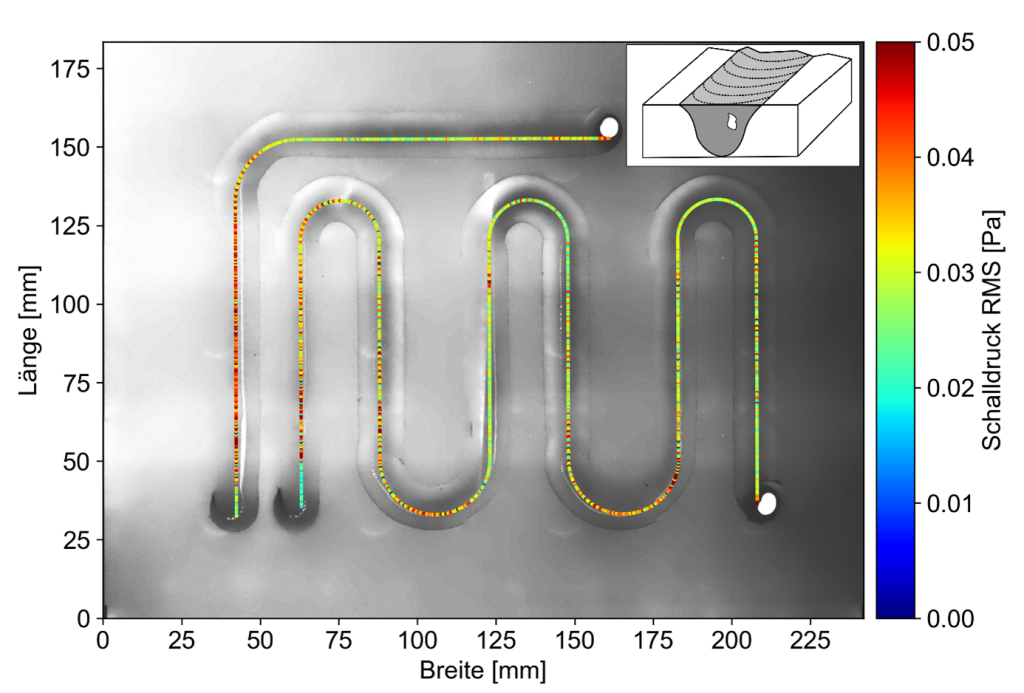
Anwendung des Datensatzes
Es wurde in der Analyse gezeigt, dass die akustischen Daten stark von den unterschiedlichen Schweißparametern beeinflusst werden. Die Daten bestätigen folglich das Zusammenspiel von Werkzeuggeometrie und Schweißparametern. Eine Korrelation zur Schweißrichtung sowie Geometrie zu den Tunnelfehlern wurde erkannt. Für die Analyse wurden Mel-Spektrogramme als Eingangsdaten und CNNs als Modell-Architektur genutzt. Im Ergebnis können Hohlräume und Gratbildung mithilfe der überlagerten akustischen Daten detektiert werden. Zusätzlich konnten die verschiedenen Verschleißzustände der Rührreibschweißwerkzeuge und Phasen des Prozesses identifiziert und mit guter Genauigkeit zugeordnet werden. Bei beiden Datensätzen wurden die meisten Fehlklassifikationen zu den benachbarten Klassen gemacht, obwohl dieser Zusammenhang nicht explizit trainiert wurde. Dies bestätigt, dass sinnvolle Informationen aus den Signalen erlernt wurden.
Die zunehmende Automatisierung der Produktion und ständig steigende Produktionszahlen bedingen eine vom Maschinenbediener unabhängige Prozesskontrolle, um Bauteilausschuss, Rüstzeiten und damit Produktionskosten zu minimieren. Eine zukunftsweisende Möglichkeit stellt dabei die Überwachung des Rührreibschweißprozesses mittels Luftschallemissionen dar, welche in der Folge eine zerstörungs- und berührungsfreie Inline-Prozesskontrolle ermöglicht [3].
Das diesem Bericht zugrundeliegende Vorhaben wurde mit Mitteln des Bundesministeriums für Bildung und Forschung unter dem Förderkennzeichen 01IS20001 gefördert. Die Veröffentlichung zu diesem Projekt finden Sie unter [3].
Für weitere Informationen oder Workshops zu diesem oder weiteren Projekten der Ilmenauer Fertigungstechnik (IFt) und der ProKI-Ilmenau wenden Sie sich gern an unseren wissenschaftlichen Mitarbeiter Kai Ehlich.
[1] Köhler T., Schiele M., Glaser M., Schricker K., Bergmann J., Augsburg K. (2020). In-situ monitoring of hybrid friction diffusion bonded EN AW 1050/EN CW 004A lap joints using artificial neural nets. Proceedings of the Institution of Mechanical Engineers. Journal of Materials, Design and Applications. 234 (5), 766–785.
[2] Zlatanovic D., Balos S., Bergmann J., Köhler T., Grätzel M., Sidjanin L., and Goel S. (2020). An experimental study on lap joining of multiple sheets of aluminium alloy (aa 5754) using friction stir spot welding. The International Journal of Advanced Manufacturing Technology, 107 (7), 3093–3107.
[3] Grätzel, M. et al. (2022). Investigation of the Directional Characteristics of the Emitted Airborne Sound by Friction Stir Welding for Online Process Monitoring. In: da Silva, L.F.M., Martins, P.A.F., Reisgen, U. (eds) 2nd International Conference on Advanced Joining Processes (AJP 2021). Proceedings in Engineering Mechanics. Springer, Cham. https://doi.org/10.1007/978-3-030-95463-5_3
Beitrag von: M. Sc. Kai Ehlich